Parylene Coating Services
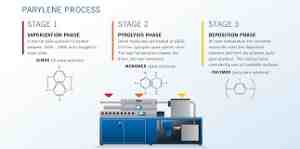
Parylene Coating Process
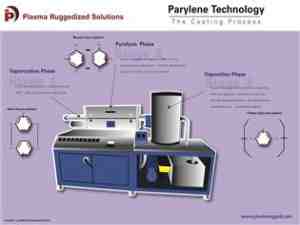
Parylene Technology - The Coating Process
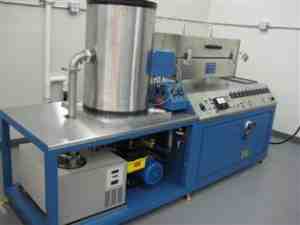
Parylene Coating System
What is Parylene Coating?
Discover the exceptional benefits of Parylene conformal coating, a cutting-edge technology used across industries to safeguard and enhance the performance of vital components, devices, and surfaces. Unlike traditional coatings, Parylene coating is created at room temperature, eliminating the need for a liquid phase during application. This unique feature enables the coating to penetrate even the narrowest spaces, as small as 0.01mm, providing comprehensive and uniform coverage.
Plasma Ruggedized Solutions offers three different types of Parylene materials: Parylene C, Parylene D and Parylene N. Dimer N is the most commonly used of the three in medical applications. We can create a thin and transparent coating that is an ideal option for optical applications. Our parylene coatings are chemically inert, biocompatible and FDA-approved for use in medical implants, and compliant with N.A.S.A’s low outgassing requirements of less than 1.0% Total Mass Loss and 0.1 CVCM (Collected Volatile Condensable Materials) or less outgassing in a vacuum environment.
Contact Plasma Ruggedized Solutions today or keep reading to find out how our Parylene conformal coating services can benefit your company’s products.
Parylene Conformal Coating Options
Parylene C
Parylene C is the sister product of Blue Spark™ Parylene Dimer and has the same high performance and high purity characteristics but without the added UV tracer material. This thin-film solution creates a Parylene conformal coating that provides excellent resistance against corrosive gases, inorganic acids, water, salt spray, bases and organic solvents. It is designed for use in harsh environments and can be paired with silicone or polyurethane to create an abrasion-resistant coating. Parylene C is cost-effective and frequently used for various aerospace and medical applications. Parylene C is more widely utilized across different industries because it is cost-effective and highly versatile.
Parylene N
Parylene N is comprised of carbons and hydrogens and has a higher dielectric strength than Parylene C. It also provides greater crevice penetration due to its higher molecular activity during deposition. For applications where visual inspection is critical such as connectors or second assembly soldering locations, a UV tracer can be added to the dimer which will allow the coating to be inspected under a standard UV light source. The addition of the UV tracer to the coating during application does not reduce the effectiveness of the Parylene Coating and does not require any additional processing during the application procedure.
Parylene D
Parylene D is comprised of carbon and hydrogen with the addition of two chlorine groups to its benzene ring which are also para-substituted. It carries properties that are similar to Parylene C but is also able to withstand high temperatures. The dielectric strength of Parylene D is lower than Parylene C or N but it provides the same level of surface resistivity.
Parylene Coating Applications
Parylene coatings are ideal for a range of applications spanning from implantable medical device coatings, to equipment designed to handle some of the deepest parts of the ocean. For medical applications, parylene is the preferred conformal coating material as it is biocompatible, with a long-tested history and little risk of complications. Additional applications for Parylene coatings include:
- Surgical devices
- Human implantable devices
- Printed circuit boards
- Various electronic equipment
- Marine applications and more.
Contact Plasma Ruggedized Solutions for more information!
Contact Plasma Ruggedized Solutions today or peruse our whitepapers today to learn more about our Parylene conformal coating services and how they can benefit your company’s products. We also offer Parylene Remediation and stripping services and various in-house testing and laboratory services.
Advantages of Choosing Parylene Coating
Parylene conformal coating is applied using a vacuum deposition process, also known as polyparaxylylene coating, that involves heating the solid Parylene dimer to a vaporous state, then re-condensing it on the target assemblies to be coated. The physical characteristics of Parylene conformal coating make it highly resistant to various hostile environments. Parylene offers many additional advantages over wet-process or dip-process conformal coating.
High Chemical Resistance and Insulative Properties
Plasma Ruggedized Solutions utilizes proprietary masking processes that ensure greater safety for the product being coated and result in superior and consistent product quality. Our vapor deposition process allows Parylene coatings to be uniform in thickness and completely pinhole free with a dielectric strength exceeding 6000 volts per mil. Parylene coating provides a water-resistant coating barrier for electronics and marine applications.
Parylene is also one of few materials approved for FDA Class 6 specifications.
Uniform Conformal Coating
Our proprietarily controlled Parylene coating services feature multistage operator and inspection points to assure high first-time yields. Our coating process ensures that the coating forms consistently over all available surfaces. The result is a clear and uniform coating with high chemical resistance and superior dielectric properties. This coating method is thinner film than other coating processes, allowing assemblies to be coated thoroughly without an increase in their size or loss of material thickness around the edges of components.
Improved Coating Durability
Parylene coating provides excellent mechanical properties and remains stable at temperatures from-200ºC to 150ºC. This coating resists the corrosive effects of acidic and alkaline materials and offers extremely high chemical and fungal resistance. The superior electrical properties of our coating methods provide an excellent barrier to gases, making it adaptable for nearly any project.
Proven Effectiveness in a Variety of Industries
Parylene penetrates easily and can adhere to a range of substrates, including glass, metal, plastic, elastomer, and more. Because of its precision application and enduring features, it is the preferred conformal coating material for military and medical customers. Some frequent industries served include:
Additional Features of Parylene Conformal Coatings
- Provides a water-resistant coating barrier for electronics and marine applications
- Resists the corrosive effects of acidic and alkaline materials
- Reduces the effects of vibration for circuit boards and other electronics
- Creates a low-stress coating that does not involve a liquid stage or require curing
- Ensures complete conformity, coating the entire assembly and leaving no areas open to exposure
- Can be coated with urethane to create an abrasion-resistant layer without affecting performance
- Meets FDA requirements and military specifications
Plasma Ruggedized Solutions offers a variety of Parylene coating services. View our FAQ section or read our whitepapers to learn more about Parylene conformal coating and other custom coating solutions. If you still have questions, please contact us to discuss our Parylene coating services.
Physical and Mechanical Properties of Parylene Conformal Coatings
There are three types of Parylene conformal coating that are frequently used: Parylene C, Parylene D and Parylene N. Parylene C is more widely utilized across different industries because it is cost-effective and highly versatile. Parylene N is next, with Parylene D being used less frequently than the others.
TYPICAL PHYSICAL AND MECHANICAL PROPERTIES | |||
Parylene (N) | Parylene (C) | Parylene (D) | |
Tensile Strength, psi | 6,500 | 10,000 | 11,000 |
Tensile Strength, MPa | 45 | 69 | 76 |
Yield Strength, psi | 6,300 | 8,000 | 9,000 |
Yield Strength, MPa | 2,400 | 3,200 | 2,800 |
Elongation at Break, % | 40 | 200 | 10 |
Density, g/cm3 | 1.110 | 1.289 | 1.418 |
Coefficient of Friction: | |||
Static | 0.25 | 0.29 | 0.33 |
Dynamic | 0.25 | 0.29 | 0.31 |
Water Absorption, % (24 hr) | 0.01 (0.019") | 0.06 (0.029") | <0.1 |
Index of Refraction, nD23 | 1.661 | 1.639 | 1.669 |
Why Work With Plasma?
While our state-of-the-art material application concepts are constantly evolving, we have always operated on four major structural pillars:
1. High-quality NADCAP, AS9100 and NASA-certified engineering services.
2. A constant drive for developing process and safety control.
3. A quality first/customer-centric mentality centered on open and honest communication.
4. Continuous improvement performance (CIP) culture for the empowerment of both our customers and employees.
Request a Quote for Parylene Coating Services
Contact Plasma Ruggedized Solutions today to learn more about our Parylene conformal coating services and how they can benefit your company’s products. We also offer Parylene tumble coating services and various in-house testing and laboratory services.