Implantable Medical Device Coating
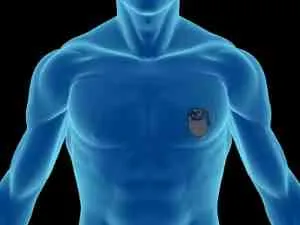
A well-known medical company approached Plasma Ruggedized Solutions regarding an implantable pacemaker device. The company had a shortage of the electronic components used in the pacemaker and could not keep their supply house stocked.
The Technical Requirements
The client needed a biocompatible medical device coating that complied with IPC J-STD-001 standards and additional requirements outlined by their manufacturer. They required a 1 mil tolerance for the urethane Parylene conformal coating application. and believed automated spray application was the only way to achieve the required precision and tolerance. Product longevity was also a priority for the client due to the medical device application.
When our engineers discussed using a hand spray application for medical device encapsulation, the client expressed concerns about human error and the ability to achieve precise tolerances and repeatability. We convinced the client to leave a few units with us to test our implantable medical device coating, completely free of charge.
The Process
After carefully reviewing the medical device company’s design and specifications, we applied Parylene conformal coating material to the units via our proprietary CVD application. Our process involves applying the coating at ambient temperatures and using specialized vacuum equipment to create a uniform thickness. The result is a hermetically sealed medical component fully protected from moisture and impact.
The Results
A few days after receiving the units, a team of several engineers, buyers, and managers from the medical organization visited our office to discuss the results. The team was shocked because they received a 100% first-pass yield on the samples we provided. This was a significant improvement over the 60-70% yield they experienced with other companies they had approached.
We achieved such precise tolerances with the biocompatible medical device coating that the team was surprised we had completed the process so quickly and with such precision. Our engineers presented a Power Point presentation and wire diagram process map delineating the macro steps of how we applied the Parylene to the implantable medical devices. coating without robots or automated processes.
The customer left approximately 20 additional units with us to see if we could achieve the same results. Once again, our specialized CVD encapsulation process produced a 100% first-pass yield. Their team was impressed that we could produce such exceptional and repeatable results without robotics and asked to observe our spray coating process.
Our precision, repeatability, and quality resulted in a 2-year relationship with the company. We helped them revise and develop their manufacturing processes and restock their facility with approximately 100,000 units.
We have a strong commitment to quality assurance and meeting the stringent guidelines required by the medical industry. Our engineering staff, teaming with our quality and production personnel are a key reason for the high first-time yield performances and the precision application of the Parylene material. lPart of our quality assurance process involves giving conformal coating sprayers several months of hands-on training before allowing them to work on client products. We go above and beyond to ensure consistency and quality in our medical device coatings.